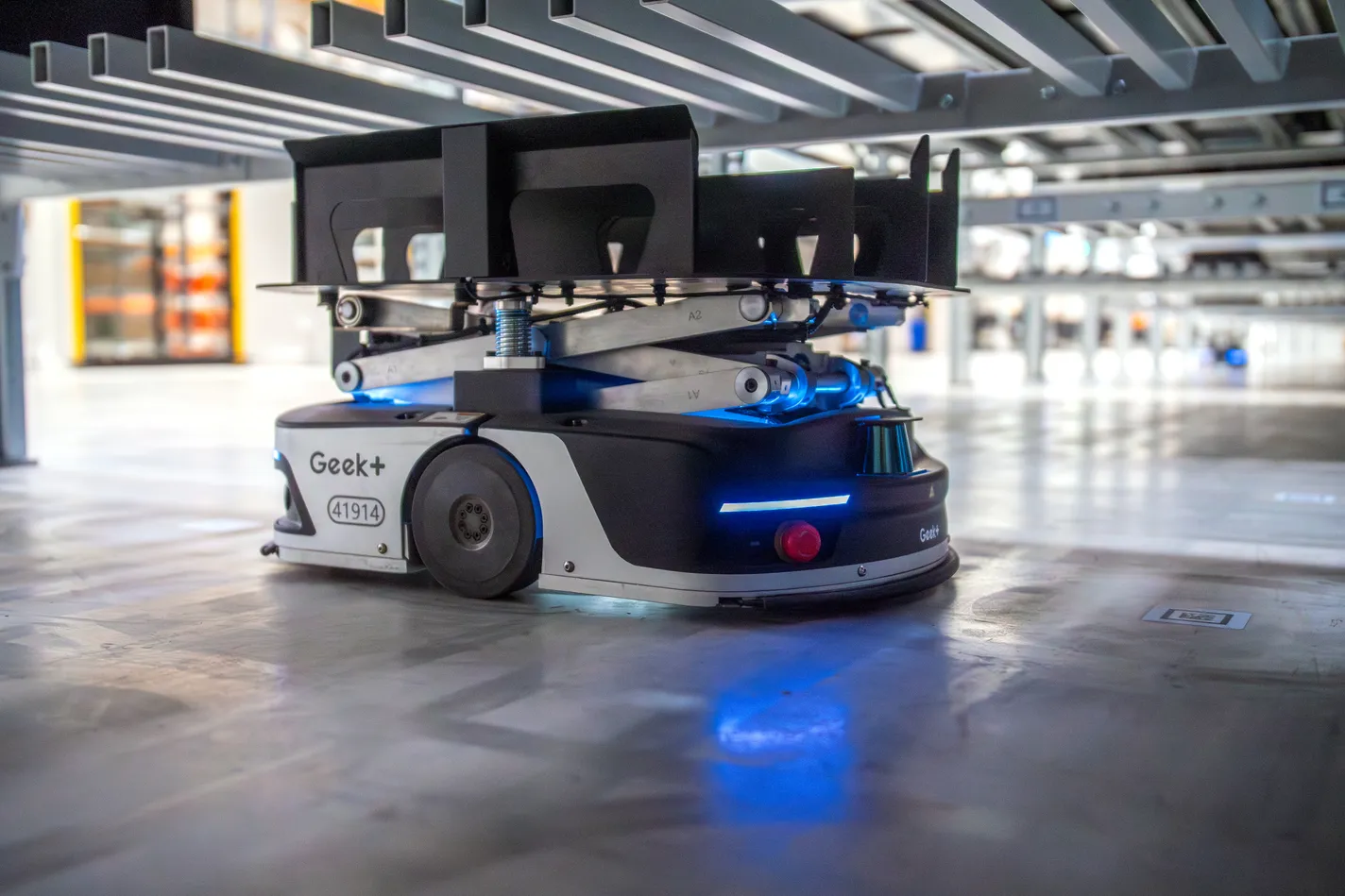
New automated robotic warehouse for Authentica Fulfillment
Authentica Fulfillment is one of the divisions of Authentica s.r.o. and is dedicated to providing outsourced logistics services for e-commerce companies. Higher efficiency of logistics operations through fulfillment center is achieved by concentrating a larger volume of shipments. Due to the significant growth in demand for its services, Authentica Fulfillment decided to increase the capacity and throughput of its warehouse in Syrovice near Brno. To ensure capacity growth and efficient shipment processing, the planned project focused on efficient use of warehouse space and the introduction of automated technology into processes, which will enable it to cope with the growing demand for these services and increase its competitiveness in a dynamic market.
Project baseline and objectives
Cardboard and pallet racking was used for storage of goods. Thus, the storage capacity of the premises was not being used efficiently. The cardboard racks were used for easier availability of goods for order picking. Each position had its own internal barcode. The unused available space above the cardboard racks limited the possibility of increasing storage capacity as the number of SKUs stored increased.
Although the internal WMS has the ability to record the dimensions of individual SKUs and calculate the occupancy of a given stock position, it was not possible to manually capture input data on dimensions due to the high number of stock cards. The WMS, due to the lack of input data, did not use the calculation module and did not have information about the actual occupancy of each position.
The picking of goods was done in the "multi-order picking" mode based on the generated list of orders to be picked for individual warehousemen. The individual items were not stored in the warehouse based on a turnover analysis and picking routes were therefore not optimally planned. To pick a particular item, it was necessary to scan the storage position, the item and the location on the picking trolley. Once the picking is complete, the order cart is handed over to the packing zone for dispatch.
The crate was scanned before the order was packed. The WMS displayed a list of items to be included in the order. By scanning the items again, the order is checked for completeness and the confirmed order can be packed and tagged with a unique QR code to clearly identify the package on the conveyor. At the end of the conveyor, the package is rescanned and a shipping label is printed and manually applied to the package according to the system data. This has led to errors where the shipping data of one package has been pasted onto another package by the warehouse clerk. Prepared packages were manually sorted onto pallets by carrier. The manual sorting also created room for error when sorting was based only on visual inspection of the shipping label.
The main objective of the operations automation project was to maximize the use of the warehouse space across the entire height and ensure sufficient capacity for the continuous development of fulfillment services and the growing number of clients. By automating the operation, Authentica Fulfillment wanted to achieve faster and more efficient order picking and shipping processes. The secondary objective of the project was to optimize the operation of the centre with less demand on human resources, which are currently unavailable on the labour market.
The overall requirements and objectives of the project were:
- efficient warehousing with maximum use of warehouse height (10 m)
- increase in storage capacity
- automation of the collection of information on the dimensions of the stored products for the calculation of the optimal use of individual storage positions
- automated checkweighing of dispatched consignments
- automated application of shipping labels
- automatic sorting of dispatched consignments
Proposed solution
The proposed solution for the logistics operation automation project was developed in cooperation between LogTech and VertiFlex, where it was a general delivery due to the system integration of the sub-technologies and their connection via the integration platform and the WCS system VertiNode to Authentica WMS, which is the company's main operational information system.
As can be seen from the objectives of the tender documentation, the proposed solution included an automated robotic warehouse, a roller conveyor with inspection, sorting and application stations and an input station for measuring and weighing new items into the warehouse system.
Storage solution
The new storage capacity was to be built on a 54x45 metre area with a usable storage height of 10 metres. In order to achieve the best utilisation of storage capacity and to reduce the cost per unit, a fully automated robotic warehouse with high stocking density was designed. The minimum required stacking density is 30,000 KLT bins with a standardised dimension of 600x400 mm with a minimum height of 280 mm and a load capacity of 30 kg. The capacity of the robotic warehouse is a minimum of 1,500 SKUs delivered for picking per hour.
The robotic warehouse is equipped with 18 RS 11 stacking and picking robots and 45 P40 underrun AMR robots from Geek+. Boxes of goods are loaded into the robotic warehouse via 23 stacking slots and transported to the transfer stations on the lower levels of the racks via the P40 robots. The P40 robots are equipped with a lifting platform for safe entry into the rack and precise removal of the prepared crate. From the transfer stations, the crates are stacked into position by RS 11 robots, which are capable of stacking into positions up to 11 metres high.
The robots are controlled by WCS VertiNode, developed by VertiFlex. VertiNode is thus also the integration platform that coordinates and controls the activities of all the other technologies delivered as part of the project. VertiNode is connected to the internal Authentica WMS, the parent control system, via an API.
Order picking and shipping
During picking, P40 robots transport individual cases from the picking stations to one of ten picking stations. The picking stations are equipped with visual marking of the destination via Pick-to-Light technology and orders are picked here. The Tote-to-Person approach has eliminated the inefficient and physically strenuous activity of long walking routes of warehouse workers "person to goods". This resulted in significant time savings and a huge increase in order picking efficiency.
The picking zone is connected to 16 workstations for packing finished orders. The picking zone and the downstream packing zone operate asynchronously because the tasks in these zones are not proportional to each other in terms of time. This also corresponds to the higher number of packing stations compared to the ten picking zones.
Packaged orders are tagged with a unique QR code and transferred to the roller conveyor of the automatic sorting line. The capacity of the conveyor is 450 packages per hour. The alignment conveyor aligns the shipments to the left side for downstream QR code retrieval using a Cognex camera. Identification of the QR code triggers the printing and sorting job. Applying the printed label to the shipment takes less than 3 seconds.
After the label is applied, the shipment passes through a checkpoint to ensure that the label is properly applied. The next checkpoint is to weigh the shipment and take a photo of the shipment to measure the volume of the shipment. After successful inspection, the consignment passes to the downstream conveyors and a set of Flowsort sortation units, which, according to the sortation data from the previous stages, ensure that the consignment is sorted into the appropriate output. The outlet is designed in the form of a gravity chute, which is terminated by a picking table. The consignments are then removed from the table for further handling (final sorting, palletisation by carrier, etc.). The chutes are equipped with fullness detection. If the sorters are full, they will not send any more shipments until the chute is released. The conveyor line is equipped with seven chutes. Five slips are for sorting shipments by carrier, one slip is for unloaded shipments, and one slip is for shipments that could not be sorted due to unavailability of an outlet or loss of tracking of the shipment on the conveyor line.
Automation of volume measurement of new SKUs
When new items are introduced into the warehouse that lack volumetric data in the system, it is required to provide this information and transfer it to the client's ERP system. The volume measurement of new items is performed by a dedicated Verti.Metric solution, which allows the volume of various objects to be weighed and measured quickly and accurately. The technology is delivered in a customised configuration according to the capacity required and the specific measuring and weighing tasks. Verti.Metric can be supplied in stationary or dynamic versions.
In a dynamic solution, the technology can be integrated into a conveyor system where information is collected on continuously passing items (goods, shipments, pallets, etc.) In the case of the Authentica project, a stationary solution was selected to provide input information to the customer's ERP system. It is therefore a stand-alone workstation that is used on an intermittent basis when new SKUs are introduced into the system, and is equipped with a Cognex camera with volume measurement function, a platform scale and a handheld scanner. The unit is designed for items ranging in size from 3.5 x 3.5 x 1.5 cm to 75 x 55 x 55 cm.
Warehouse control system VertiNode
VertiNode is a dedicated control and integration platform for automated logistics. It is compatible with most warehouse systems and is developed by VertiFlex's in-house software team. In this project, the VertiNode warehouse control system communicates with the parent WMS and provides two-way information exchange between the control system of each technology and the WMS.
All warehouse operations are managed by the in-house WMS, which was developed to meet the needs of Authentica Fulfillment. The VertiNode integration platform is a suitable solution for the client's requirements for comprehensive management of the delivered technology while connecting to Authentica's main operational information system. Connection to Authentica's WMS is via a REST API. VertiNode manages the delivered technology independently of the client WMS and provides the necessary functionality:
- ABC turnaround analysis to minimize KLT/carton travel distance to the picker.
- MIS/MES software to manage picking with connection to the current Authentica WMS
- APS software for efficient order planning and picking
- CMMS software for managing the maintenance of delivered equipment
The WMS manages the collection of order information and passes this information to a subordinate system, within which the picking and removal of orders to delivery points takes place. This information is then passed back to the WMS, which solely manages the packing and dispatching within all parts of the warehouse.
Conclusion
With the new automated warehouse, Authentica Fulfillment has increased its warehouse capacity to 2.5 million shipments per year. The innovative automated warehouse solution compensates for the labour shortage in the market. The total investment of EUR 3 million has a calculated payback period of three years.
At the end of the project, the entire solution underwent a rigorous testing and stress testing process to ensure that all operations run smoothly even under maximum traffic load during seasonal peaks. After the pilot phase, the entire system is connected to the proper operation of the entire warehouse. Integrating all parts of the system into one functional unit was a major challenge. Many years of experience in automation and integration on the part of the supplier companies LogTech and VertiFlex contributed to its implementation. On the other hand, it was the enlightened approach to automating operations on the part of Authentica Fulfillment and the maximum cooperation of all parties involved.
The new robotic warehouse, which is equipped with 63 robots (18 RS 11 order picking and picking robots and 45 P40 underrun AMR robots), can currently handle 20,000 orders per day and the goal is to reach a level of 500,000 orders per month. The warehouse currently provides logistics services for more than 50 e-shops. With the new automated warehouse, Authentica Fulfillment has become the outsourced logistics service provider with the most extensive robotization in the country.